5月11日,位于中山市黄圃镇的格兰仕北厂区车来车往,一辆辆货车满载出发,前往南沙港等港口,将“新鲜出炉”的高端洗碗机销往全球各地。
“15秒可完成一台高端洗碗机内胆的组装,年产洗碗机达150万台。”格兰仕洗碗机制造基地相关负责人介绍,公司在2022年引进行业顶尖的6条洗碗机自动化生产线后,人工减少四分之三的同时,效率提升了30%。基于各类指标,格兰仕洗碗机数字化智能化示范车间被认定为2022年中山市制造业企业数字化智能化示范车间。
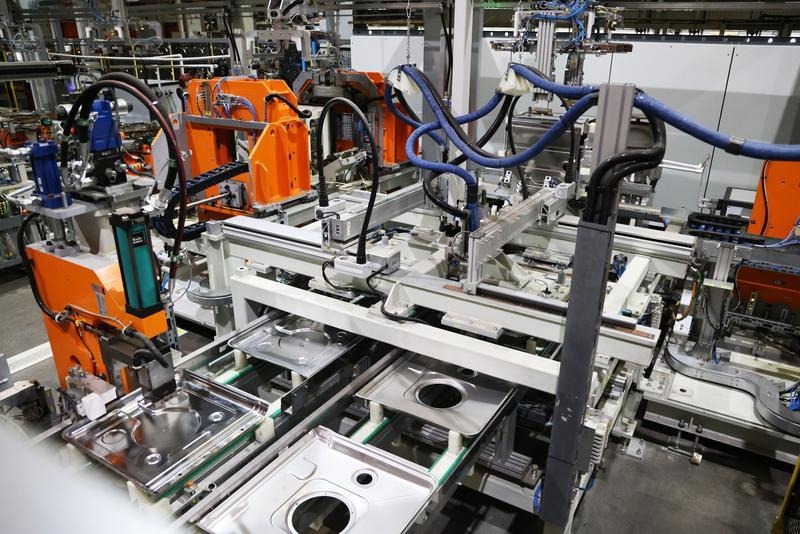
顶尖洗碗机车间向“黑灯工厂”迈进
顺着指引,记者来到格兰仕中山基地北厂区。门口一侧的宣传牌上,标题为“格兰仕领先全球的洗碗机智能制造”的中英文解说简短而清晰。
“怎么这么少人?车间内的光线也不太好?”面对记者的疑问,工作人员打开所有照明开关,沿着车间通道边走边道出其中的缘由:“全自动生产线几乎不用人工,为确保设备正常运转和产品质量,每条生产线最多配一名工程师,所以,很多时候连照明设备都不用开启,趋向于‘黑灯工厂’。”
这条代表全球领先水平的全自动内胆生产线长约25米,主要包括焊接和铆接工序。洗碗机的制造包含拉伸、冲压成型、切边、翻边和检验五道工序,此前,各道工序都是独立的,单工序至少需要一名工人,如今自动化设备“合五为一”,从上料到五金件的传输都由机械手替代,工人减少四分之三,效率提高30%。
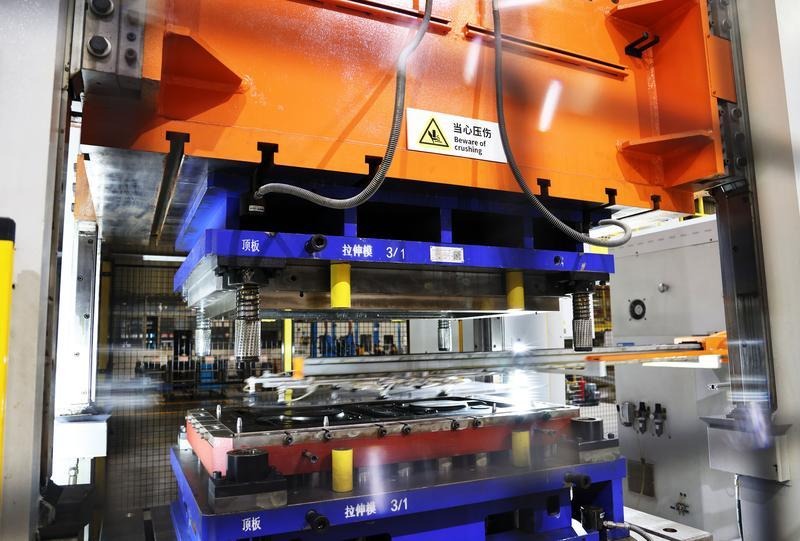
据悉,近年来,格兰仕全面推动增资扩产,2022年新增6条洗碗机自动化生产线,包括4条全自动冲压线、1条洗碗机内胆焊接铆接线和1条碗篮生产线。格兰仕的新增洗碗机全自动装配线代表行业最先进智造水平,实现中板自动折U,顶板、底板自动打胶,中板和底板自动组装咬合,前支撑架自动装配铆接等工序自动组装成内胆等工序,单线15秒内可完成一台高端洗碗机内胆的组装,产品直通率提高到99.9%,极大提升产能的同时,为满足市场新增的定制化、绿色化、高端化、智能化需求创造了条件。
“数字化智能化不可能一次到位,它是一项不断完善的系统工作。”格兰仕洗碗机制造基地相关负责人告诉记者,从2014年开始,格兰仕中山基地每年围绕传统制造业与信息化、智能化融合,持续引进行业领先的智能化装备,不断升级和改造。从长远来看,“黑灯工厂”是一种趋势。
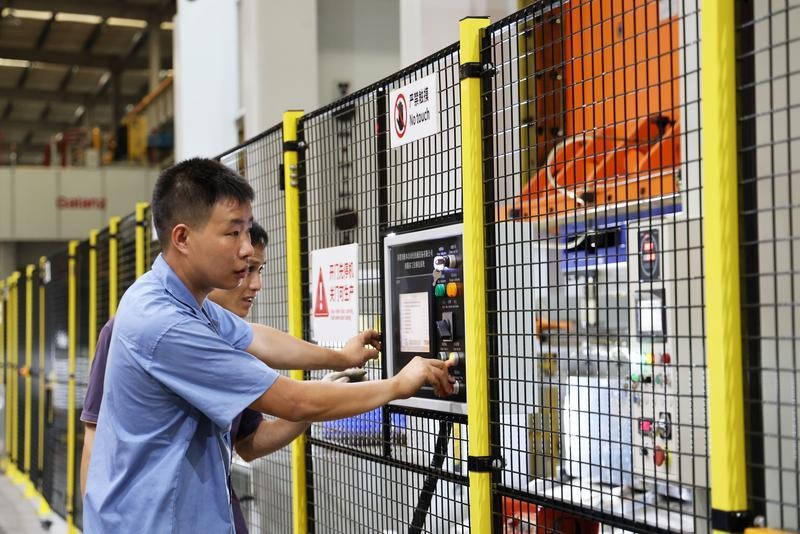
一体化信息系统让所有数据畅通交互
“真正意义上的数字化智能化工厂,光有自动化设备是远远不够的,只有构建全产业链一体化信息系统,才能将数字化智能化工厂推至一个较高的水准。”该负责人介绍,格兰仕一方面加速推进智能制造基地建设,一方面打通智能制造全产业链的“最后一公里”,通过自主芯片实现产业链供应链自主可控。首款芯片“BF2”于2020年正式量产并应用到格兰仕微波炉等家电产品中,第二款芯片“NB2”也已经在国家新基建项目投入使用。
与此同时,通过打造高度一体化的全链路数字化系统,格兰仕从传统的“接单—研发—生产—交货”模式,转变为供应、生产、销售、用户一体化的工业互联网生态,以洗碗机生产为例,销售接到订单到研发、供应、生产,以前要通过手工作业或邮件传达,流程繁琐,沟通时间长,而一体化信息系统打通各个环节,实现数据互通,一名计划员就可以完成上百种物料的调度和跟进工作,整体效率提升多倍以上。
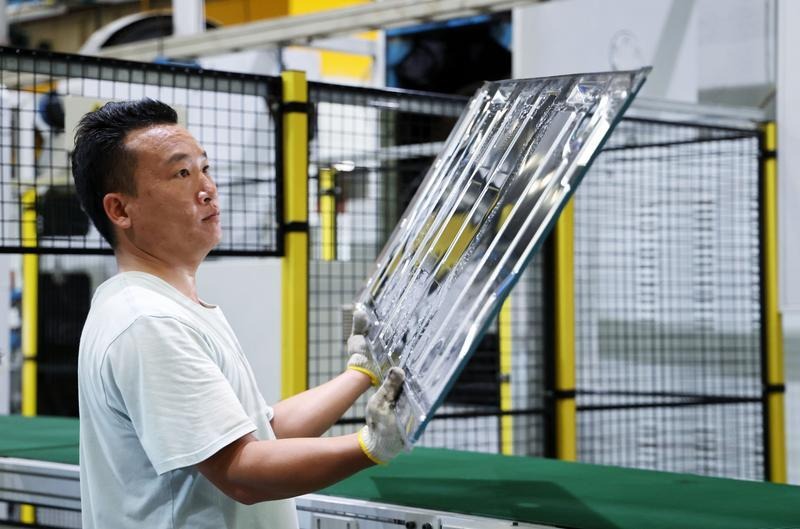
格兰仕通过工艺数字化、装备智能化、过程管理数字化等先进手段, 构建全产业链一体化信息系统。通过自动化、信息化、标准化、透明化的可追溯智能生产模式, 确保产品质量、缩短产品生产周期和研发周期、减少报废以及库存等造成的资源浪费。以 ERP 管理系统为核心,通过生产设备数据自动采集、过程追溯、生产管理、生产可视化等功能实施,实现生产过程管控优化。
数字化转型最主要的挑战是如何解决人才短缺、人才适配的问题,企业要转型升级,人才也要转型升级,从顶尖专家到基层技工都要参与整个生产制造转型。“人是格兰仕第一资本。从制造向智造转型,并不是简单的机器换人,而是以产业升级带动人才升级。”格兰仕集团董事长兼总裁梁昭贤指出,产业技工是格兰仕全产业价值链智能制造的重要一环。
据悉,格兰仕以人才为中心推进数字化转型,以数字升级不断赋能传统制造。在推进全产业链智能化、数字化升级的进程中,一方面,在全产业链全面推行全员技工化制度,打造自主研发的自动化工程师团队;另一方面,围绕解决制造业“卡脖子”的问题,充分发挥产业链龙头带动作用,在全球各地寻找芯片领域科学家,组建芯片以及集成电路设计、研发、应用等领域人才队伍,将智能化、数字化自主权牢牢掌握在自己手中。
编辑 曾淑花 二审 蓝运良 三审 苏小红