11月2日,记者从深中通道管理中心获悉,我国钢结构行业最具权威性的5A级全国性社会组织——中国钢结构协会于近日召开第十三届太平洋钢结构会议暨2023中国钢结构大会。会议上,由深中通道管理中心牵头申报的《跨海集群工程桥隧钢结构智能制造关键技术研究及应用》项目获“2023年度中国钢结构协会科学技术奖特等奖”。
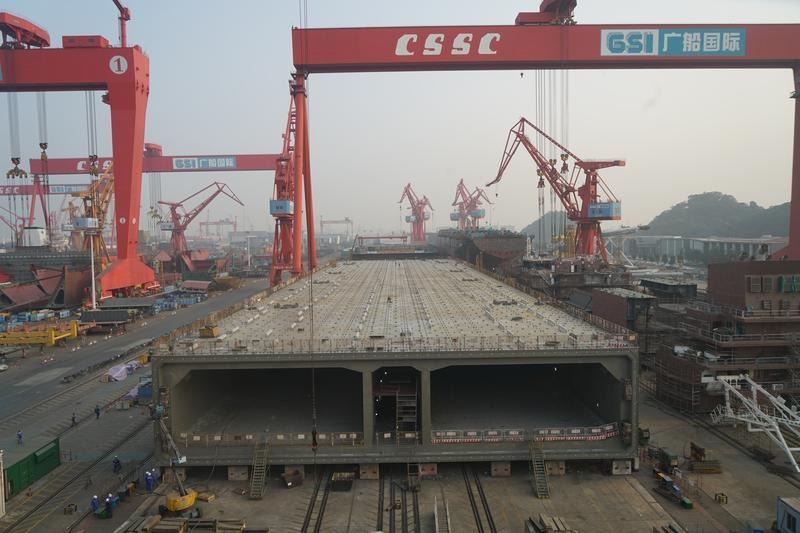
该奖项由国家科学技术奖励工作办公室批准,中国钢结构协会于2007年设立。此次获奖,是中国钢结构协会对深中通道推动我国钢结构领域科学技术进步作出突出贡献的充分肯定,也是对项目大力推行智能建造所取得成果的高度认可。
深中通道是集“桥、岛、隧、水下互通”于一体的跨海集群工程,全长约24公里。项目主要构造物(海底隧道钢壳-混凝土沉管和海中长桥)均为钢结构,总用钢量达60万吨,传统制造工艺已难以满足超大规模、优质高效的要求。为此,项目积极响应“中国制造2025”(国家行动纲领),结合当前信息技术的发展,对钢结构制造理论、设备和工艺进行创新,全面实施智能制造,实现“提质、增效、降本”的目标。
针对跨海集群工程桥隧钢结构智能制造共性关键技术问题,项目开展了智能制造理论、装备、关键技术和工程应用研究,取得了四项主要创新成果:
一是创建了跨海集群工程桥隧钢结构“智能制造四线一系统”技术体系,实现了钢结构生产全过程智能控制和管理。与传统工艺相比,综合效率提升20%以上,油漆消耗降低约15%,焊接一次合格率提高到99%以上,一次喷涂合格率提高到99%以上。
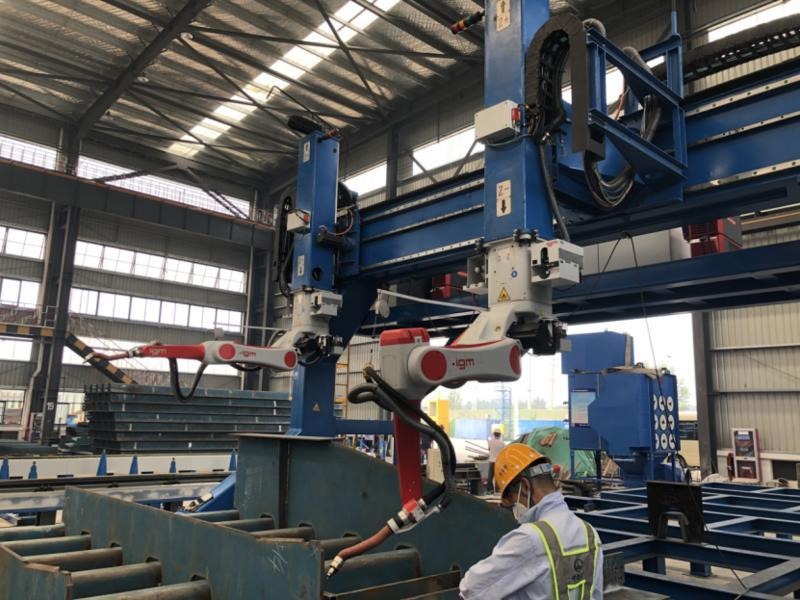
二是研发了基于结构特征和视觉识别的复杂构件机器人混合编程技术,构建了焊接机器人工艺知识库,突破了板材/型材智能切割生产线互联互通、多门架多机器人协同控制、复杂环境下机器视觉识别、机器人离线路径与工艺规划、装备及生产信息异构数据统一建模等系列关键技术,焊接效率提升15%,人员减少60%。
三是攻克了超宽、变宽沉管钢壳特殊材质厚板高精度制造关键技术及三维测控方法,管节46米宽度方向端头精度比设计要求提高50%,165米长度方向精度比设计要求提高50%;采用FCB焊接技术实现了厚度40毫米高强度钢Q420C钢板批量化焊接,构建了基于国产三维建模软件的可视化焊缝三维地图,实现了焊缝信息三维可视化展示和建管养一体化管理。
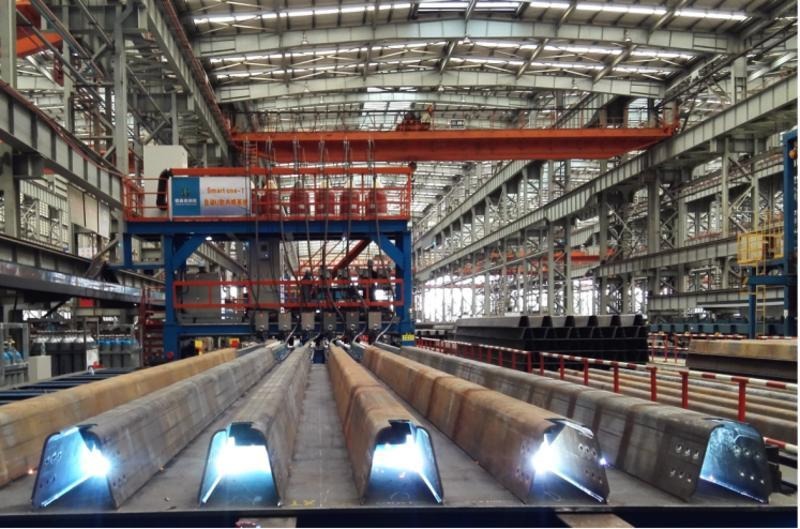
四是研发了正交异性钢桥面板U肋双面埋弧全熔透焊接关键技术,阐明了焊接方法及工艺参数对疲劳性能的影响机制,建立了相关的制造技术标准和质量验收标准,使纵肋与顶板焊接构造细节的疲劳设计强度由80兆帕提高到125兆帕。
值得注意的是,该项目成果获授权发明专利33项、软件著作权5项,编制团体标准4部,发表论文33篇,出版专著3部,显著提升了我国桥隧钢结构智能制造的国际竞争力,在深中通道60万吨钢结构建造过程中得到成功应用,并推广应用于黄茅海跨海通道等10余项国家重点工程,取得了显著的社会效益和经济效益。
编辑 曾淑花 二审 魏静文 三审 徐小江